Plastics recycling and the circular economy of plastics are buzz words in the industrial sector today for a good reason. Plastic manufacturing is estimated to increase by 40% over the next 10 years and if we don’t do anything about plastic sustainability, the oceans will carry more plastic than fish, by weight, before the year 2050. If this alarming estimate is true, experts warn that marine life will be irreparably damaged. Coral reefs will be destroyed and the food supply that so many around the world rely on will be irrevocably damaged. Plastic component manufacturers around the world are looking to find the solution to this problem, with some focusing on producing 100% recyclable parts from the design phase.
Â
One such company, RD Industries, has expertly designed an entire line of plastic components, called the OneFlo™ chemical dispensing product line which is manufactured to be 100% recyclable. RD Industries’ OneFlo™ product line consists of two subproducts: OneFlo™ Cap Adapters and OneFlo™ Bottle Inserts. Read on to learn more about the benefits of utilizing 100% sustainable plastic components, as well as more information on the OneFlo™ product line.
What Are the Benefits of Using 100% Sustainable Plastic Components
Plastic manufacturing is a critical component of nearly every socioeconomic class. Plastics manufacturing provides environmental sustainability and provides the potential for inherent recyclability and energy recovery options. If you are in the plastics manufacturing industry or you are purchasing plastic components, you have likely heard of the Three Pillars of Sustainability. For plastics, these pillars are environmental, economic, and social sustainability. 100% sustainable plastic components are sustainable in all three areas:
1. Environmental Sustainability: a small percentage of the world’s oil production is utilized for plastic production (only about 4%). Plastics are an excellent material choice for environmental sustainability because they are durable and lightweight – making them a great choice for strength without adding energy to move the components they make up due to excess weight. Plastics become even more environmentally sustainable when they are designed to be recyclable upfront. Designing recyclability into a plastic component is the key to providing the ultimate environmental sustainability. RD Industries’ OneFlo™ plastic chemical dispensing component product line is designed to be 100% recyclable.
2. Economic Sustainability: plastic manufacturing makes a positive impact on both the macro and micro-economies globally and locally. Many countries like China, the United States, Germany, Brazil, and Japan all rely heavily on plastic manufacturing for their macro-economies. The global plastics market value was estimated to be almost 580 billion U.S. dollars in 2020 and is forecasted to surpass 750 billion U.S. dollars by 2028. Therefore, the plastics manufacturing market makes up a significant share of the global economy. But plastic components also make sense on the microeconomic scale. Since plastic components are so cost-effective to produce and it is easy to produce complex shapes, they are an excellent method to keep costs low without sacrificing quality. They also boast excellent material properties and lower maintenance costs over similar materials, reducing the lifetime cost savings.
3. Social Sustainability: plastic companies across the globe employing more than 180k people. Plastics industries are typically more technologically advanced and with that tends to come more social inclusivity and diversity. Plastic products also make for a safer world. They are utilized in lifesaving devices such as airbags, shock absorbers, and even bicycle helmets. Plastics are also
utilized in the medical industry, playing a critical role in modern-day healthcare for applications such as medical containers, blood bags, surgical gloves, tubing, artificial blood vessels, and more.
OneFloâ„¢ Cap Adapters
One of the biggest safety hazards when utilizing chemicals has always been changing bottles of chemicals over before they are completely empty. The older systems can potentially lose prime, causing the chemical to leak, exposing employees to potential safety issues. RD Industries created the OneFloâ„¢ Plastic Cap Adapter to solve the problem of potential safety hazards when changing bottles of chemicals over before they are empty. The OneFloâ„¢ Cap Adapters allow a superior flow rate while maintaining complete containment of the chemical in the container prior to and after application. They contain no metallic parts, strengthening their chemical compatibility. The cap adapter boasts a cross-slit valve that prevents the chemical line from emptying when you are changing chemicals; this innovation ensures no chemical contact and an overall reduction in waste.
These sustainably manufactured cap adapters enable you to completely reseal the container of chemicals after opening them. They are also compatible with all OneFloâ„¢ Bottle Inserts. Moreover, when you pair the OneFloâ„¢ Cap Adapters with the OneFloâ„¢ Bottle Inserts, you achieve the best seal for chemical containment and dispensing on the market.
Are you looking for a plastic chemical containment manufacturer who can provide you with excellent products to save you money and improve the safety of your personnel?
Contact the experts at RD Industries to learn more about our innovative OneFloâ„¢ products today.
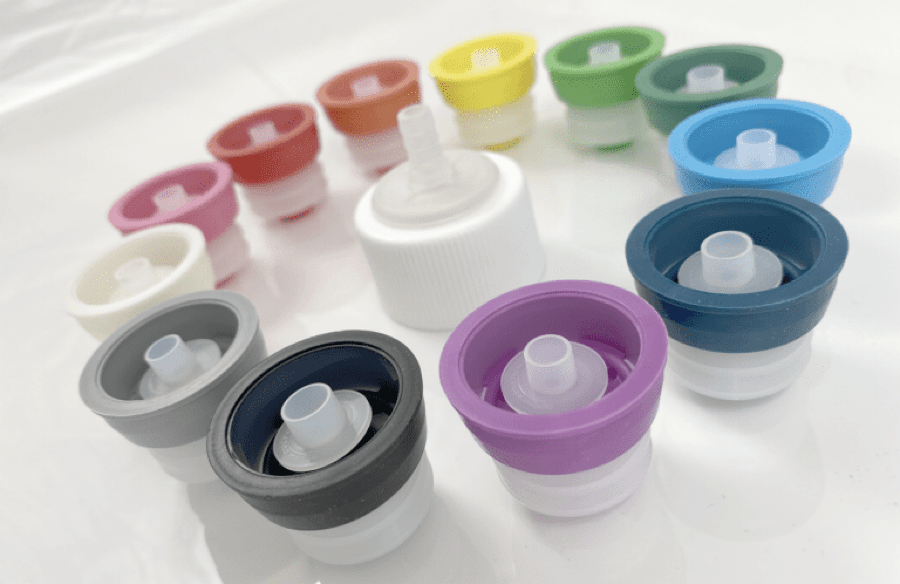
OneFloâ„¢ Bottle Adapters
Chemical containers have a tendency to panel or bloat due to improper venting and off-gassing. RD Industries has created the OneFlo™ Bottle Inserts to provide a sustainable solution that to this problem. The OneFlo™ Bottle inserts are also compatible with any RD Industries cap, and they offer the latest in Closed-Loop technology. RD Industries is proud to say that this is the world’s first line of recyclable and sustainably manufactured bottle inserts for chemical containment and dispensing. The design boasts a bi-directional valve that provides optimal venting and off-gassing. The softseal around the plug and over the neck finish areas offers a superior seal for dispensing and transport alike. With 32 metering options, you are sure to find the dilution you need.
The bottle insert system works in a straightforward manner. The valve in the bottle insert is completely sealed until a compatible cap is connected which pushes the valve to establish chemical dispensing. When the cap is removed, the valve slides up and re-seals.
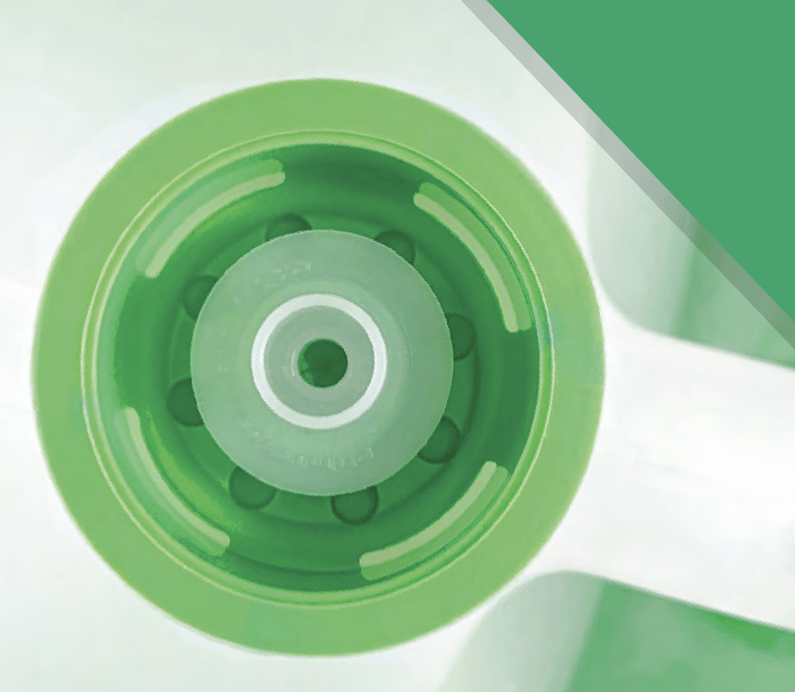
RD Industries wants to be your partner in advanced chemical and containment systems. Contact RD Industries at 1-402-455-8553 to learn more about how we can provide you with the best chemical containment systems.
At RD Industries, we make Connections for a Safer Planet. Since 1968, we have been at the forefront of innovation in the fluid containment and dispensing industry. Our CEO and Founder, Rod Laible, has more than 60 patents to his name for product design and process. Rod’s motto spans multiple industries, with varying degrees of application: to keep the world safe. This motto is apparent in the products he has designed and launched through RD Industries.
At RD Industries, we have been the proven leader in the design, manufacture, and distribution of containment and dispensing systems for decades. We are proud to serve customers throughout North America, Central America, South America, Europe, and the Asia Pacific. Our key market is chemical packaging which is utilized for chemical dispensing of cleaning solutions. We are based in Omaha, Nebraska. Our world-class team of product designers, engineers, and professionals expertly brings our products to realization and we remain ahead of the game as innovators. We look forward to working with your team soon.